RojoRacing
Donut Powered Wise-guy
Ok so this is happening today and I'll taking lots of pictures as I go along so maybe I'll actually post a DIY thread here for everyone to learn. This is going on the drive wheel of my Enve for use on the rear of the Trek but the process is the same no matter what wheel you want to make covers for.
Ok first thing you'll need to do is order some finished Carbon Fiber plate, this means it's cured carbon and not raw carbon weave. You'll need 0.008"(0.20mm) thick carbon, this is as thin as you can go but if you can't get it this thin up to 0.012"(0.30mm) thick will also work fine and be honestly be more durable and easier to work with at the cost a little more weight. The covers made out of 0.008" will weight 180 grams for both, that's not much. The only place I've found online that sells the size I need is ACP Composites which just happens to be down the street from me (lucky me) but also ships world wide. You'll need 24"x 48" to do both sides of one wheel.
https://store.acpsales.com/products...x-48-2x2-twill-carbon-fiber-sheet-gloss-matte
The carbon will have a protective clear tape on one side, that's you're glossy side, the other unprotected side is your matte finished side.
My original covers for the V20 I choose to have the matte finish facing out which I really like for the stealthy look but for these wheels we'll be exposing the glossy side. First thing you'll need to do is lay down some masking tape because it's nearly impossible to write fine lines on bare carbon. I'm using 3" wide painters tape, the wider the better because you'll need less runs of tape to cover the whole thing. If you can find a lighter color do it because pencil is hard to see on blue.
Next thing you'll want to do is start drawing the lines for where to cut. My covers are about 22" in diameter but each different wheel depth will need a different size cover so treat 22" as a ball park starting point. Find a center point where your lines wont run off the edges but try and fit them in the corner so you have large whole pieces left over. Also make sure to mark your center point after you find it so you can find it again, trust me I lost it a few times when making my first covers. If you're not totally sure what exact diameter will work best for your wheel then draw several lines in 1/4" increments , pencil lead is cheap. Do the same thing for the center hole cutout. If you're making cover for a non drive wheel with rim brake the center hole can be just large enough to fit over the hub. If you're making covers for a drive wheel or non drive wheel with disc brake rotor start with a small circle but make sure to do enough to reach out to 4.5". more on this later.
After you're done drawing all your circles so grab your handy heavy duty scissors, oh did you forget to buy some? I use these micro serrated scissors because they grip that slick glossy carbon as they cut but even quality smooth blades will get the job done. https://www.scissorsonline.com/8-straight-stainless-trimmer-serrated.html Yes you can cut the carbon with just scissors, this stuff is barely thicker then paper.
You'll want to cut out your covers starting with your largest circle because you can trim off more later but you can't put more back on. Measure twice cut once or be ready to start all over.
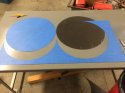
Ok first thing you'll need to do is order some finished Carbon Fiber plate, this means it's cured carbon and not raw carbon weave. You'll need 0.008"(0.20mm) thick carbon, this is as thin as you can go but if you can't get it this thin up to 0.012"(0.30mm) thick will also work fine and be honestly be more durable and easier to work with at the cost a little more weight. The covers made out of 0.008" will weight 180 grams for both, that's not much. The only place I've found online that sells the size I need is ACP Composites which just happens to be down the street from me (lucky me) but also ships world wide. You'll need 24"x 48" to do both sides of one wheel.
https://store.acpsales.com/products...x-48-2x2-twill-carbon-fiber-sheet-gloss-matte
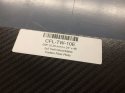
The carbon will have a protective clear tape on one side, that's you're glossy side, the other unprotected side is your matte finished side.
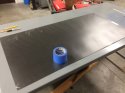
My original covers for the V20 I choose to have the matte finish facing out which I really like for the stealthy look but for these wheels we'll be exposing the glossy side. First thing you'll need to do is lay down some masking tape because it's nearly impossible to write fine lines on bare carbon. I'm using 3" wide painters tape, the wider the better because you'll need less runs of tape to cover the whole thing. If you can find a lighter color do it because pencil is hard to see on blue.
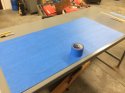
Next thing you'll want to do is start drawing the lines for where to cut. My covers are about 22" in diameter but each different wheel depth will need a different size cover so treat 22" as a ball park starting point. Find a center point where your lines wont run off the edges but try and fit them in the corner so you have large whole pieces left over. Also make sure to mark your center point after you find it so you can find it again, trust me I lost it a few times when making my first covers. If you're not totally sure what exact diameter will work best for your wheel then draw several lines in 1/4" increments , pencil lead is cheap. Do the same thing for the center hole cutout. If you're making cover for a non drive wheel with rim brake the center hole can be just large enough to fit over the hub. If you're making covers for a drive wheel or non drive wheel with disc brake rotor start with a small circle but make sure to do enough to reach out to 4.5". more on this later.
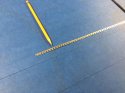
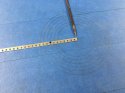
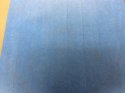
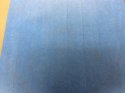
After you're done drawing all your circles so grab your handy heavy duty scissors, oh did you forget to buy some? I use these micro serrated scissors because they grip that slick glossy carbon as they cut but even quality smooth blades will get the job done. https://www.scissorsonline.com/8-straight-stainless-trimmer-serrated.html Yes you can cut the carbon with just scissors, this stuff is barely thicker then paper.
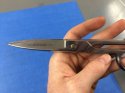
You'll want to cut out your covers starting with your largest circle because you can trim off more later but you can't put more back on. Measure twice cut once or be ready to start all over.
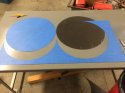
Attachments
Last edited: